What is the difference between chain and belt conveyor?
Chain conveyors and belt conveyors are both used for material handling, but they differ in design, function, and applications:
1. Basic Structure
Feature | Chain Conveyor | Belt Conveyor |
---|---|---|
Driving Mechanism | Uses metal chains (roller, flat-top, etc.) driven by sprockets. | Uses a continuous rubber/fabric belt driven by pulleys. |
Surface | Chains with attachments (slats, flights, or hooks). | Smooth or textured belt surface. |
Flexibility | Rigid, suited for heavy loads. | Flexible, can handle inclines/declines. |
2. Key Differences
A. Load Capacity
- Chain Conveyor:
- Handles heavy, bulky, or abrasive materials (e.g., pallets, metal parts, scrap).
- Used in automotive,Daily/Foods/Tobacco/Logistic industry, and heavy industry.
- Belt Conveyor:
- Best for lighter, uniform materials (e.g., boxes, grains, packages).
- Common in bulk food, packaging, and logistics.
B. Speed & Efficiency
- Chain Conveyor:
- Slower but more durable under stress.
- Used for precision movement (e.g., assembly lines).
- Belt Conveyor:
- Faster and smoother for continuous flow.
- Ideal for high-speed sorting (e.g., parcel distribution).
C. Maintenance & Durability
- Chain Conveyor:
- Requires regular lubrication and chain tension checks.
- More resistant to heat, oil, sharp objects And Flexible
- Belt Conveyor:
- Easier maintenance (belt replacement).
- Vulnerable to tears, moisture, and slippage.
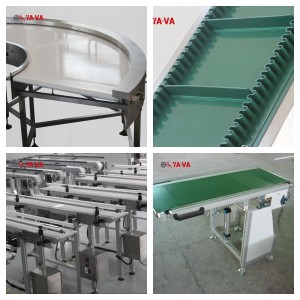
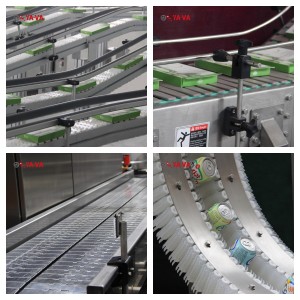
3. Which One to Choose?
- Use a Chain Conveyor if:
- Moving heavy, irregular, or after package goods
- Need high durability
- Use a Belt Conveyor if:
- Transporting light to medium-weight, uniform items.
- Require quiet, fast, and smooth operation.Routinely used for bulk food
4. Summary
- Chain Conveyor = post-packaged food ,Heavy-duty, industrial, slow but strong.
- Belt Conveyor = bulk food,Light-duty, fast, flexible, and low maintenance.
How many types of conveyor chains are there?
Conveyor chains are categorized based on their structural design and operational purpose. Below are the primary types with specific use cases:
1、Roller Chains
Structure: Interlocking metal links with cylindrical rollers
Applications:
Automotive assembly lines (engine/transmission transport)
Heavy machinery transfer systems
Capacity: 1-20 tons depending on strand configuration
Maintenance: Requires regular lubrication every 200-400 operating hours
2、Flat Top Chains
Structure: Interlocking plates forming continuous surface
Applications:
Bottling/packaging lines (food & beverage)
Pharmaceutical product handling
Materials: Stainless steel or FDA-approved plastics
Advantage: Easy cleaning with CIP systems
3、Plastic Modular Chains
Structure: Molded polymer links with snap-fit design
Applications:
Washdown food processing
Electronics assembly (ESD-safe versions)
Temperature Range: -40°C to +90°C continuous operation
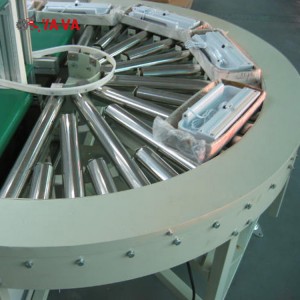
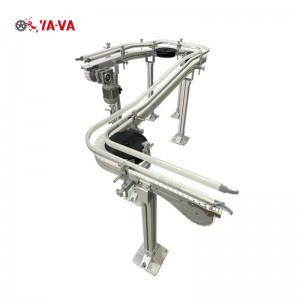

Applications:
Forklift mast guidance
Industrial lift platforms
Durability: 3-5x longer lifespan than standard chains in cyclic loading
5、Drag Chains
Structure: Heavy-duty links with attachment wings
Applications:
Cement/powder material handling
Wastewater treatment sludge conveying
Environments: Withstands high moisture and abrasive materials
Selection Criteria:
Load Requirements: Roller chains for >1 ton, plastic chains for <100kg
Environmental Conditions: Stainless steel for corrosive/wet environments
Speed: Roller chains for high speed (>30m/min), drag chains for slow movement
Sanitation Needs: Plastic or stainless flat top chains for food contact
Each chain type serves distinct industrial needs, with proper selection being critical for operational efficiency and equipment longevity. Maintenance schedules vary significantly between types, from weekly lubrication (roller chains) to annual inspections (plastic modular chains).
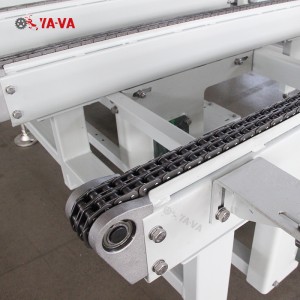
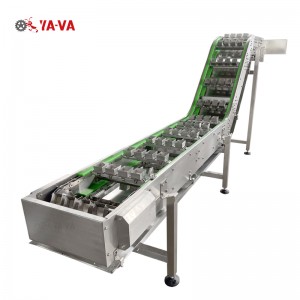
Post time: May-16-2025